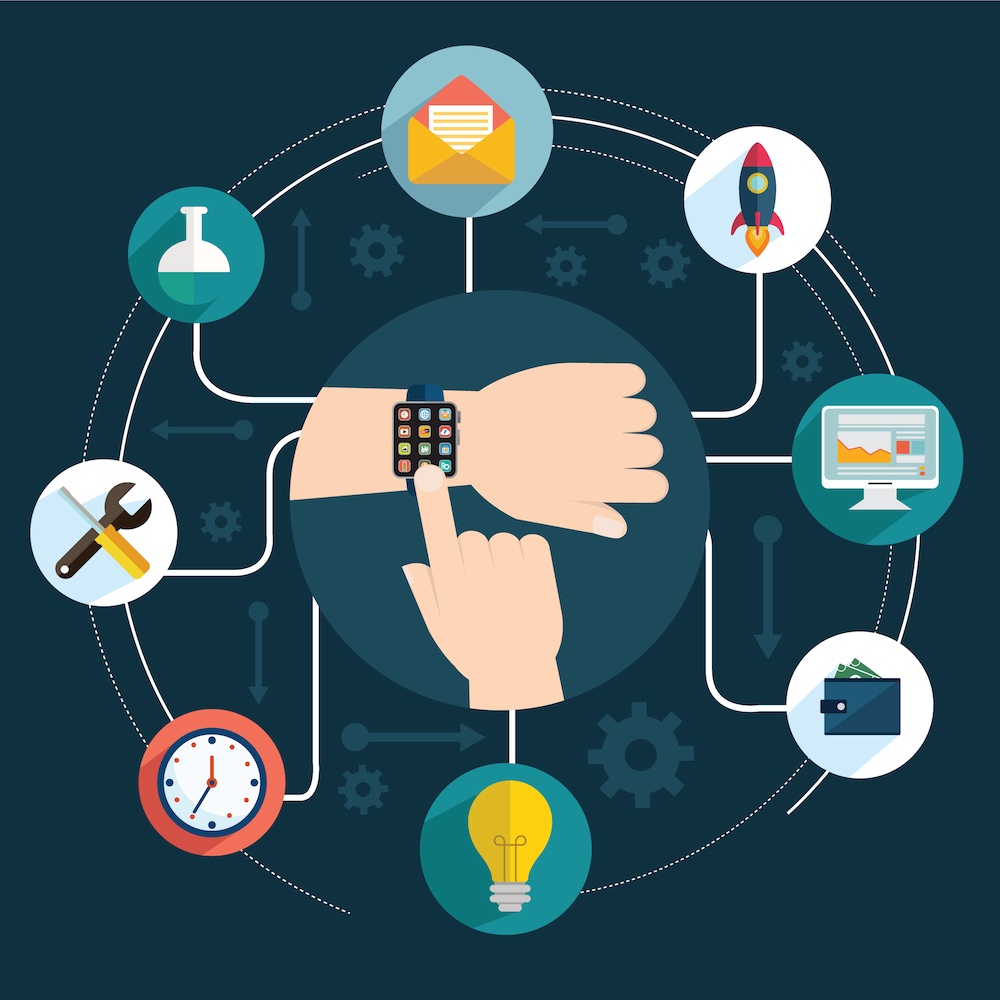
Accelerating Time-to-Market in OEM Manufacturing with MES
In today’s competitive landscape, Original Equipment Manufacturers (OEMs) must meet growing demands while reducing production cycles. Achieving faster time-to-market has become critical for staying ahead. MES (Manufacturing Execution Systems) plays a vital role in optimizing processes, improving efficiency, and reducing delays in OEM manufacturing. This blog explores how MES software accelerates time-to-market while enhancing overall performance.
The Growing Importance of Time-to-Marke
Time-to-market refers to the time it takes to develop, produce, and deliver a product to consumers. For OEMs, reducing this timeframe ensures competitiveness, customer satisfaction, and profitability. Yet, achieving this without sacrificing quality or increasing costs remains a challenge.
- OEMs often face complex supply chains, demanding customers, and resource constraints.
- Faster production cycles require precise coordination between design, production, and delivery teams.
Here, MES software emerges as a game-changer by streamlining operations and eliminating inefficiencies.
How MES Drives Time-to-Marke
MES software connects every aspect of production, ensuring real-time visibility and seamless coordination. This leads to faster and more efficient operations.
- Streamlined Production Processes
MES eliminates manual tracking, reducing errors and delays. Automated workflows enhance productivity across every stage of manufacturing. - Real-Time Data Visibility
With MES, OEMs gain access to real-time data for monitoring operations. This helps identify bottlenecks and make quick decisions. - Quality Assurance
MES integrates quality checks at every step, minimizing rework and ensuring faster approvals.
Key Benefits of MES in OEM Manufacturing
The advantages of implementing MES software extend beyond time-to-market. Let’s explore the top benefits:
1. Enhanced Collaboration Across Teams
MES ensures that all teams, from design to production, stay aligned with clear communication and data sharing.
- Engineers can adjust designs based on production feedback instantly.
- Managers can monitor progress and adapt plans in real time.
2. Reduced Lead Times
Automated scheduling, real-time tracking, and predictive maintenance significantly reduce production delays and lead times.
- MES schedules tasks efficiently to avoid resource conflicts.
- Predictive tools identify potential breakdowns before they occur.
3. Improved Supply Chain Coordination
MES integrates with supply chain systems, ensuring timely delivery of raw materials and components.
- Suppliers receive alerts for replenishments automatically.
- MES minimizes production halts caused by supply chain disruptions.
Case Study: MES Accelerating Time-to-Market
Challenge
An automotive OEM struggled to meet increasing demand due to outdated production tracking methods and frequent delays.
Solution
The company implemented MES software across its manufacturing plants. The system automated workflows, enhanced quality checks, and provided real-time insights.
Results
- 30% reduction in production cycle time.
- Significant improvement in on-time deliveries.
- Enhanced product quality with integrated inspection systems.
This case highlights the transformative impact of MES on reducing time-to-market.
Models for Accelerating Operational Excellence with MES
Several operational models combined with MES implementation can further drive efficiency:
1. Lean Manufacturing with MES
Lean principles aim to eliminate waste. MES complements lean manufacturing by providing real-time data and streamlining workflows.
- MES identifies inefficiencies and monitors performance continuously.
- Lean principles ensure resources are used optimally.
2. Agile Manufacturing Enabled by MES
Agile manufacturing emphasizes flexibility to meet changing demands. MES ensures adaptability by enabling rapid production changes.
- Production schedules adjust dynamically based on market trends.
- Teams respond faster to new orders with minimal downtime.
3. Just-in-Time (JIT) Manufacturing with MES
JIT reduces inventory costs and waste by producing only what’s needed, when it’s needed. MES facilitates JIT operations seamlessly.
- MES monitors inventory levels to trigger timely replenishments.
- Accurate scheduling ensures resources arrive exactly when required.
Overcoming Challenges in MES Implementation
Despite its benefits, adopting MES software can be challenging. Addressing these obstacles ensures successful deployment:
- Integration Issues: Aligning MES with legacy systems requires careful planning and robust technical support.
- Change Management: Training employees and ensuring acceptance of new systems is critical for smooth transitions.
- Cost Concerns: While MES implementation requires investment, its long-term savings justify the upfront costs.
OEMs must work with experienced partners to overcome these challenges effectively.
Conclusion
Accelerating time-to-market is crucial for OEMs to stay competitive in today’s fast-paced environment. By leveraging MES software, manufacturers can streamline operations, reduce delays, and improve collaboration across teams. From enhanced quality control to dynamic scheduling, MES empowers OEMs to meet market demands efficiently.
As the manufacturing landscape evolves, embracing MES becomes essential for driving growth and operational excellence. Ready to accelerate your time-to-market? Explore MES solutions tailored to your needs today!
Comments are closed