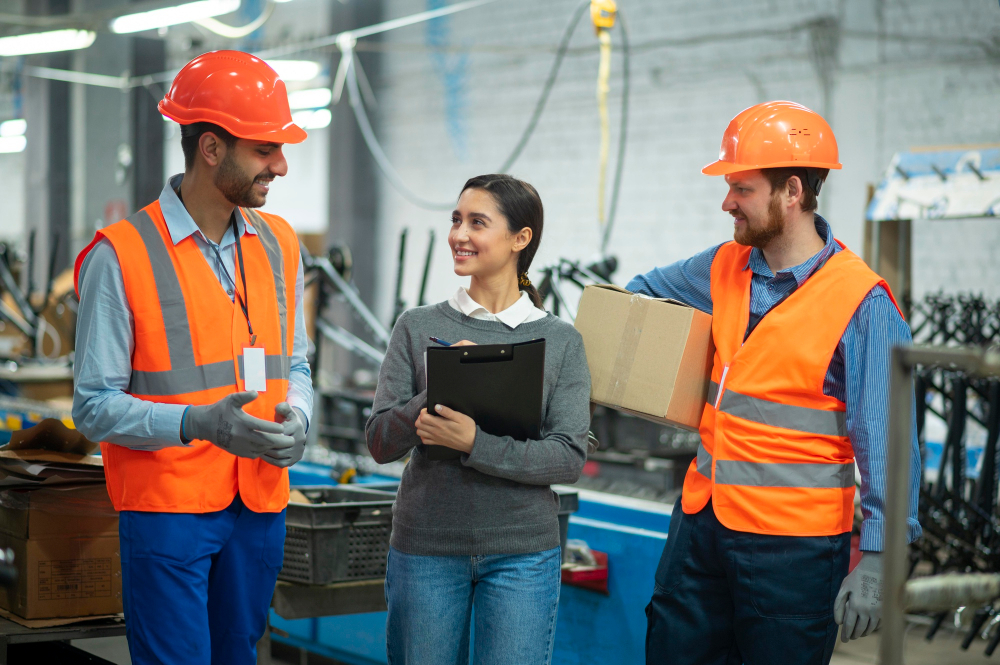
How MES Software Optimizes Job Work Manufacturing
Manufacturers handling small batch and custom orders face challenges in efficiency, quality, and cost control. Unlike mass production, job work manufacturing requires flexibility, precision, and real-time tracking. MES (Manufacturing Execution System) software plays a crucial role in streamlining operations, optimizing resources, and ensuring seamless production workflows. This blog explores how MES software improves efficiency and accuracy in small-batch and custom-order manufacturing.
The Challenges of Small Batch and Custom Manufacturing
Custom manufacturing involves frequent changes in design, material, and process requirements. Unlike traditional mass production, small-batch manufacturing requires agility and quick decision-making. However, manufacturers often struggle with:
- Frequent setup changes that lead to downtime.
- Inconsistent production tracking due to manual processes.
- Higher operational costs from inefficient scheduling.
- Complex quality control due to varied specifications.
Without a structured system, managing these variables becomes challenging. This is where MES software makes a difference.
How MES Software Optimizes Job Work Manufacturing
MES software bridges the gap between design, production, and quality control. It enhances manufacturing efficiency by providing real-time visibility, automating workflows, and ensuring compliance.
1. Real-Time Production Monitoring
MES offers real-time tracking of every order, ensuring full visibility across production stages.
- Operators receive instant work instructions.
- Managers track job progress and adjust schedules dynamically.
2. Efficient Scheduling and Resource Allocation
Small-batch production requires quick transitions between different jobs. MES optimizes scheduling, reducing setup time and resource waste.
- Automated scheduling prevents delays and bottlenecks.
- Workloads are balanced based on machine availability.
3. Improved Quality Control
Custom orders require strict quality standards. MES integrates quality checks at every stage, reducing defects and rework.
- Automated alerts ensure corrective actions before issues escalate.
- Digital records improve traceability and compliance.
4. Seamless Data Integration
MES connects with ERP systems, ensuring smooth coordination between procurement, production, and logistics.
- Operators access real-time order specifications.
- Inventory updates automatically as materials are used.
Key Benefits of MES in Small Batch Manufacturing
MES software provides significant benefits for job work manufacturers handling diverse and custom orders.
1. Increased Flexibility
MES allows manufacturers to adapt quickly to customer requirements, ensuring seamless production transitions.
- Custom orders are processed with minimal disruption.
- Operators receive updated work instructions instantly.
2. Cost Reduction
Optimized workflows and reduced waste lower production costs. MES ensures that resources are used efficiently.
- Energy and material waste are minimized.
- Labor efficiency improves with better scheduling.
3. Faster Turnaround Time
MES reduces lead times by eliminating manual bottlenecks and automating repetitive tasks.
- Orders move faster through production lines.
- Delivery times improve, enhancing customer satisfaction.
4. Enhanced Compliance and Reporting
Industries with strict regulations benefit from MES’s automated compliance tracking.
- Every batch is logged digitally, ensuring audit readiness.
- MES generates reports for regulatory and client requirements.
Case Study: MES in Custom Manufacturing
Challenge
A precision manufacturing company struggled with delays in fulfilling custom orders due to manual tracking and frequent setup changes.
Solution
The company implemented MES software to automate scheduling, track real-time job progress, and integrate quality control.
Results
- 25% reduction in production downtime.
- 30% improvement in order accuracy.
- Faster turnaround times with real-time job tracking.
This transformation highlights how MES streamlines small-batch and custom manufacturing operations.
Best Practices for Implementing MES in Job Work Manufacturing
To maximize the benefits of MES software, manufacturers must follow strategic implementation steps.
1. Define Production Goals
Identify key challenges and set clear objectives for MES adoption.
- Focus on reducing lead times and minimizing waste.
- Align MES features with business needs.
2. Train Teams for Seamless Adoption
A well-trained workforce ensures a smooth transition to MES-driven workflows.
- Provide hands-on training to operators and managers.
- Encourage continuous learning and adaptation.
3. Integrate with Existing Systems
MES should connect with ERP, PLM, and IoT systems for full process visibility.
- Ensure seamless data exchange between production and business operations.
- Use MES analytics to drive continuous improvements.
4. Monitor and Optimize Performance
Regular assessment helps in fine-tuning MES for optimal efficiency.
- Use real-time dashboards for continuous monitoring.
- Adjust workflows based on MES-generated insights.
Conclusion
Small-batch and custom-order manufacturing require precision, flexibility, and efficiency. MES software empowers manufacturers by streamlining scheduling, improving quality control, and reducing lead times. With real-time visibility and automated processes, job work manufacturers can meet customer demands efficiently while minimizing costs.
Implementing MES transforms small-batch production into a scalable, agile, and competitive advantage. Ready to optimize your custom manufacturing process? Explore MES solutions today!
Comments are closed